
04/06/2023
Di seguito pubblico alcune delle mie esperienze complete di foto e video sulle tecniche di handling che reputo più interessanti.
Per alcuni argomenti particolarmente estesi ho aperto dei post dedicati (vedi related post).
=========================================================================================
Anche tu (progettista, fornitore, utilizzatore) puoi postare di seguito dei commenti con le tue esperienze oppure con richieste di approfondimenti. E' sufficiente che ti registri nella TECHNICAL AREA
=========================================================================================
INDICE:
SGV Self Guided Veichle : carrelli elevatori a guida automaticaVoicePickingToSGV
AIV Automatic Intelligent Veichle
Magazzino Automatico Multiprofondità L-Raider
Software per magazzino WMS
Trasloelevatori
Magazzini verticali
Magazzini compattabili
Picking dinamico
Impilatori pallet vuoti
Photogallery - watch pictures
05/02/2012 - Load Planner Software
01/07/2020 - Mobile Racks Warehouses
Forum dedicato ai carrelli elevatori.
Link : Forum Macchine
Posted by admin at 18/04/2022 02:51
Navetta Inerziale che trasporta 10 pallet per ciclo
Esempio navigazione sicura in ambiente promiscuo (fiera)
Posted by admin at 25/06/2015 00:28
Voice Picking To SGV
Questa straordinaria tecnica è basata sull' interfacciamento di:
- un software WMS
- un modulo Voice Pick
- un sistema SGV.
DESCRIZIONE GENERALE:
Uno o più carrelli elevatori AGV a forche provvedono ad ottimizzare tutte le fasi di spostamento AUTOMATICAMENTE.
Gli addetti possono rimanere nelle aree assegnate guidati in tutte le funzioni di picking via voice e quindi con entrambe le mani disponibili per il prelievo.
CICLO TIPICO:
- l' SGV preleva il pallet vuoto;
- l' operatore raggiunge la posizione di inizio picking pronunciando il check digit letto sulla scaffalatura;
- l' SGV raggiunge l' operatore proprio davanti alla coordinata di inizio picking e solleva il pallet all' altezza di lavoro ottimale;
- l' operatore esegue la riga di picking (o più righe nel caso di ordine batch) seguendo le istruzioni ricevute in cuffia e confermando o rettificando le quantità via voice;
- l' SGV si sposta automaticamente alla posizione successiva regolando eventualmente l' altezza delle forche. L' operatore lo segue ed intanto riceve l' istruzione di prelievo;
- dopo la conferma del check digit della nuova ubicazione si ripetono le fasi 4 e 5;
- quando il ciclo di picking per quell' operatore è completato il carrello SGV si allontana automaticamente verso un' altra area di picking servita da altro operatore oppure verso la destinazione che può essere un' area a terra, a blocco o scaffalata;
PECULIARITA'
I carrelli SGV operano in ambiente promiscuo con totale sicurezza grazie ai laser scanner che "spazzolano" l' ambiente circostante rilevando i punti di riferimento fissi che servono alla navigazione ed i soggetti in movimento che attivano le politiche di sicurezza durante il movimento. Praticamente il carrello "sta attento" a tutto quanto si muove attorno e regola di conseguenza la velocità, gli avvisatori luminosi ed acustici, fino all' arresto se ostacoli non previsti o in movimento si avvicinano troppo.
Il sistema VOICE usa una tecnologia esclusiva che riconosce qualsiasi linguaggio senza necessità di memorizzare la voce di ogni operatore, rendendo possibile l' inserimento immediato di operatori temporanei. Le informazioni vengono trasmesse all' operatore mediante una serie di voci umane selezionabili, anzichè una voce digitale, garantendo una migliore comprensibilità e gradevolezza.
Il dispositivo a cintura misura 68x127mm e pesa appena 260 grammi.
E' resistente alle cadute anche sul pavimento ed è testato per estreme condizioni di temperatura, polvere, umidità. E' dotato di tasti a membrana (ma tutti i comandi possono essere impartiti via voce), robusta connessione cablata con le cuffie e trasmissione bluetooth per cuffie ed eventuale scanner.
Collegamento automatico di diverse aree di picking anche lontane e servite da diversi operatori.
title: Pick-n-go pick and go pick&go pik to agv
Posted by admin at 04/06/2023 19:09
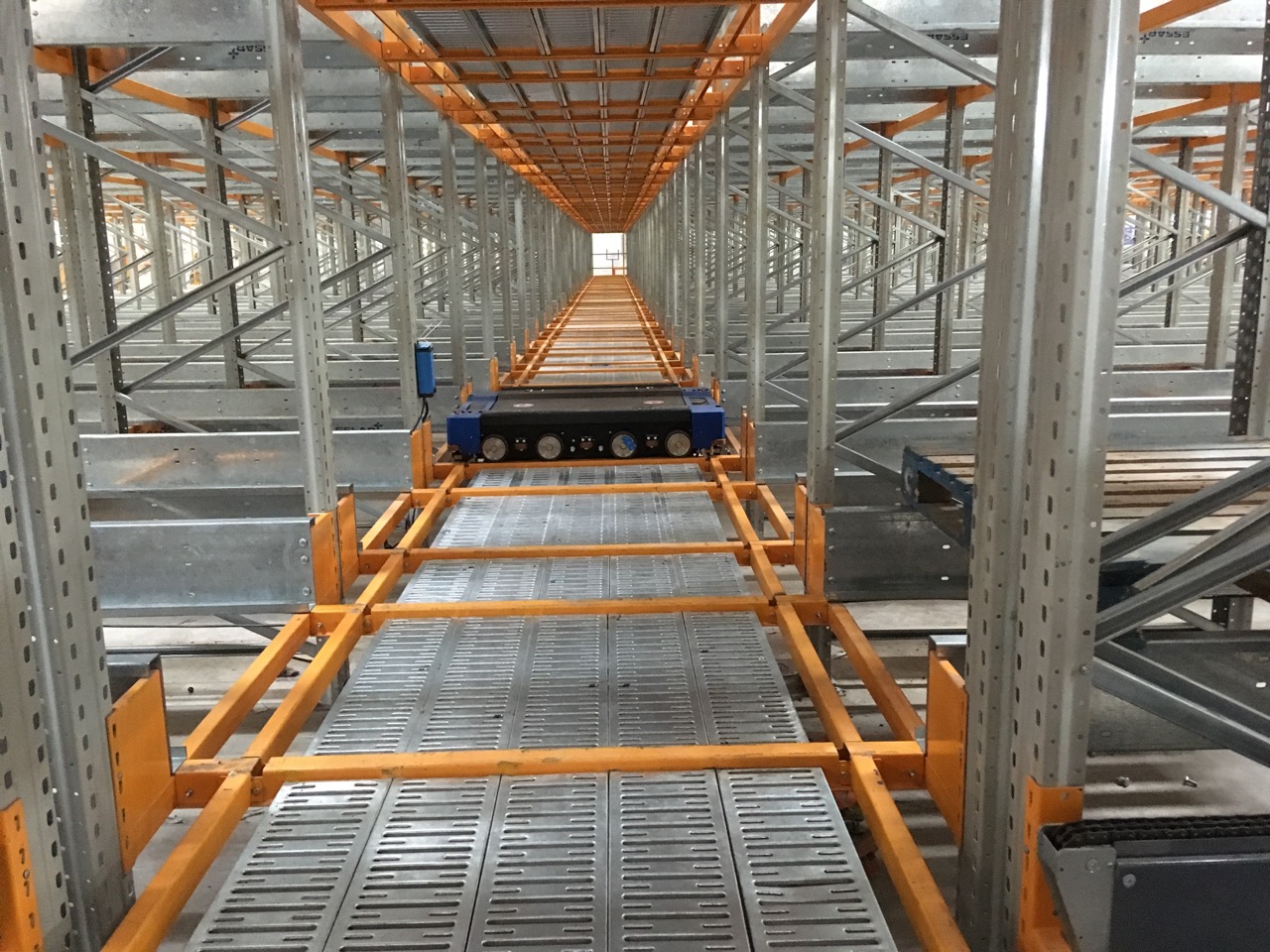
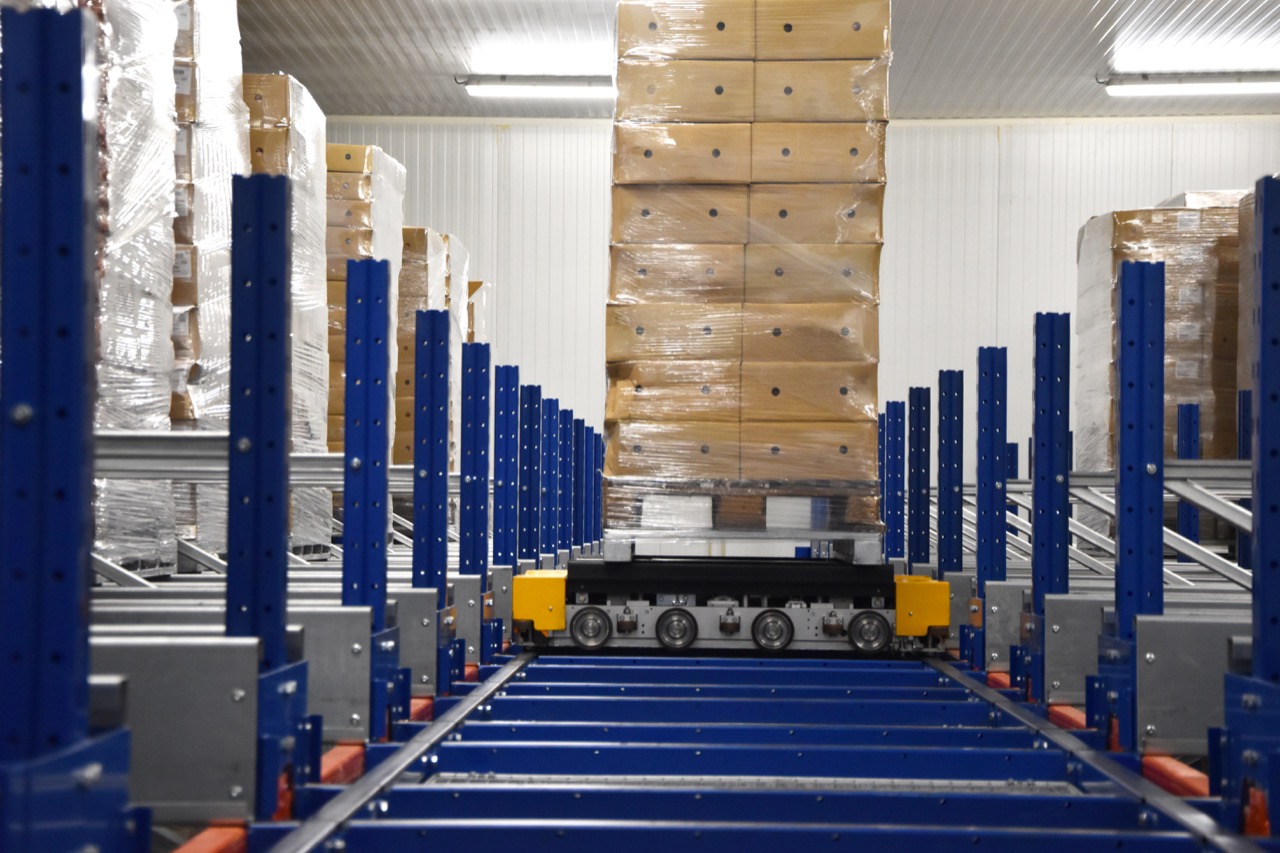
Posted by admin at 05/06/2023 17:56
AUTOCLIMBER
Innovativo modulo composto da un navetta che scorre appesa ad un fronte della scaffalatura ed un transpallet automatico che introduce o preleva il pallet da entrambi i fronti della scaffalatura.
E' un sistema meno invasivo e generalmente più economico rispetto ad un trasloelevatore.
L' applicazione perfetta è lo stoccaggio in multiprofondità con altezze limitate a 12-13 metri di altezza, dove un trasloelevatore convenzionale è decisamente poco conveniente.
VANTAGGI PECULIARI :
- con questo sistema spesso si riesce a guadagnare un livello di carico rispetto ad un impianto con trasloelevatori sia con forcole che con satellite;
- diversamente dai trasloelevatori, l' automazione non richiede la legatura in sommità pertanto si possono realizzare impianti dislocati su due capannoni con differenti altezze e/o con passaggi di travature, canali, tubi;
- in caso di stoccaggio in multiprofondità, il pallet viene inforcato dal lato corto, avvantaggiando la capienza e il display (numero di articoli affacciati) rispetto ai traslo con satelliti che normalmente gestiscono il pallet dal lato lungo.
- i pallet in entrata e uscita vengono depositati su semplici postazioni a terra oppure su rulliere.

Il sistema può essere applicato anche a scaffalature esistenti, previo verifica ed adeguamento strutturale al primo filare.
L' installazione è molto più agevole rispetto ad un impianto traslo:
- durante la costruzione delle macchine, si installano le scaffalature, le guide e la blindosbarra di alimentazione;
- le macchine arrivano su un pallet semovente, il software è pronto a bordo macchina, in una giornata di lavoro si possono già eseguire i primi movimenti
title: lraider, l-raider, raider
Questo sistema, tecnicamente denominato WMS (acronimo di Warehouse Managment System), migliora le performances dei magazzini sia in termini di capienza netta (riduce l’indice di vuoto), sia in termini di ottimizzazione del tempo uomo. E' utilizzabile in ogni area della Vs. Azienda come anche presso eventuali siti periferici.
Vengono garantiti i seguenti servizi:
- tracking delle operazioni di movimentazione
- aumento della capacità del magazzino (riduzione dell’indice di vuoto)
- elaborazione di statistiche precise su tutti i flussi di movimentazione
- gestione del first-in first-out e dei lotti di produzione
- ottimizzazione del display di picking in base alle rotazioni, riduzione dei tempi di prelievo
- ottimizzazione delle liste di prelievo
- controllo incrociato degli errori di movimentazione
- suddivisione logica del materiale direttamente in ubicazione
- eventuale pubblicazione di informazioni sul WEB e-o gestione remota del sistema a diversi livelli di accesso
Il sistema si avvale di una piattaforma base e da una serie di personalizzazioni che lo integrano perfettamente nella realtà operativa del Cliente. Questo si ottiene con una micro analisi dei flussi logistici e la predisposizione di procedure e maschere apposite.
Il software in tutte le sue maschere è multi lingua; sono già installate : italiano, inglese, francese, tedesco.
Può essere facilmente interfacciato ai PLC di governo locale di eventuali impianti di automazione.
Il software già installato in diversi magazzini da me realizzati nel corso degli anni si chiama SLIM2K.
Prima di affrontare la definizione e descrizione delle funzionalità offerte e gestite con SLIM2K e l’analisi delle modalità possibili di movimentazione della merce in un magazzino qualsiasi, è bene richiamare alcuni termini ed aspetti fondamentali di logistica.
L’ottimizzazione di un magazzino si traduce nel conoscere quanto di ogni prodotto è disponibile in un dato momento, dov’è ubicato, come reperirlo per evadere, nel tempo più breve possibile, l’ordine del cliente. In altre parole gestire al meglio sia i flussi di entrata, provenienti dai fornitori, che quelli di uscita verso i clienti.
Con un numero elevato di articoli o con grosse quantità di prodotto la gestione di un magazzino richiede anche l’introduzione di strumenti tecnologici e informatici necessari alla sua ottimizzazione, tra i quali elenchiamo i più significativi:
- Codifica e identificazione della merce con bar code;
- Mappatura delle aree di magazzino in modo univoco, fino alla singola Locazione;
- Utilizzo di Terminali Portatili con lettori bar code, meglio se collegati in real time (radiofrequenza);
- Un Software specializzato e dedicato alla gestione Logistica del Magazzino;
Con questi prerequisiti, un magazzino può essere gestito in modo puntuale ed efficiente al fine di ottenere notevoli risparmi di costi in termini di:
- Riduzione scorte. La conoscenza puntuale delle reali giacenze in magazzino permette una riduzione delle scorte necessarie a parità di soddisfazione del cliente;
- Riduzione dei tempi. La localizzazione precisa e univoca del prodotto e la conseguente possibilità di ottimizzazione degli ordini di prelievo, permettono tempi di evasione degli ordini molto più veloci;
- Maggiore capienza. La possibilità di posizionare e stoccare la merce in modalità random, mantenendone comunque la tracciabilità e reperibilità, e l’introduzione di criteri di ottimizzazione degli spazi, producono il risultato di una maggiore capienza fisica del magazzino a parità di spazio disponibile;
- Maggiore efficienza. Il parziale “scollegamento” dell’attività in magazzino dalle capacità “mnemoniche” degli operatori e la standardizzazione delle operazioni di versamento, prelievo e spostamento della merce, producono maggiore efficienza nell’attività dei magazzinieri oltre a maggiore flessibilità delle risorse umane impiegate;
- Completa tracciabilità. Tutte le operazioni e flussi vengono tracciati per prodotto, per operatore, per tipo di transazione.
SLIM2K è un software specializzato e mirato alla gestione dei flussi logistici aziendali, di magazzino e di produzione, frutto di 20 anni di esperienza nell’utilizzo del codice a barre in ambito industriale e commerciale.
L’insieme delle operazioni logistiche di un magazzino sono state codificate e articolate in un Percorso Logistico composto da una successione di cinque fasi:
-> Accettazione Materiali (entrata merce)
-> Versamento a magazzino (o stoccaggio)
-> Movimentazione Interna (o spostamento)
-> Prelievo (o picking)
-> Spedizione (con o senza spunta)
Di seguito viene riproposta a titolo esemplificativo una rappresentazione grafica di tre di esse.
Posted by admin at 21/12/2020 18:40
TRASLOELEVATORI
Si tratta di "carrelli" automatici guidati a terra ed in sommità tramite monorotaia.
A terra un sistema di traversine livella in perfetta planarità un profilo tipicamente di tipo ferroviario (burback) i cui tratti vengono saldati mediante un lungo procedimento per garantire un unico profilo senza soluzione di continuità.
Le scaffalature sono legate sopra da carpenterie atte a creare un unico blocco monolitico che deve anche mantenere la propria deformazione in ogni condizione di carico entro 1/1000 dell' altezza complessiva del magazzino (nel caso di magazzini autoportanti, la tolleranza deve essere anche verificata sotto azione di vento e neve) altrimenti i trasloelevatori, che hanno la corsa delle forcole predeterminata, troverebbero i pallet in posizione diversa nelle diverse condizioni generando errori di posizionamento progressivi con il rischio di incidenti giacchè non vi è operatore a bordo che può recuperare con l' occhio le differenze. Sotto la legatura viene fissata la monorotaia superiore che vincola il trasloelevatore in alto.
Per queste caratteristiche le macchine possono raggiungere altezze e velocità nettamente superiori rispetto ai carrelli elevatori trilaterali ai quali si sostituiscono proprio quando l’ altezza del magazzino supera i 12-13 metri o il tempo ciclo di ogni macchina deve essere inferiore ai 2-3 minuti.
Compatibilmente con la stabilità delle merci da movimentare, tipicamente filmate, è possibile raggiungere velocità operative elevatissime e quindi movimentare grandi quantità di UDC per turno di lavoro.
Il posizionamento orizzontale e verticale è affidato a PLC ed encoder assoluti o telemetri laser e complessi sistemi di fotocellule e controlli.
I trasloelevatori movimentano per mezzo forcole telescopiche le UDC che ricevono e restituiscono da sistemi di trasporto a rulli e catenarie anch’essi completamente automatici. L’elevato grado di automazione rende il sistema molto rigido ai cambiamenti delle UDC, dei tempi ciclo, delle logiche di funzionamento.
L’ assenza di operatori a bordo delle macchine permette che il magazzino sia completamente segregato. L’accesso è consentito ai soli addetti per la manutenzione; l’apertura di un solo cancello perimetrale comporta il blocco del sistema e l’interruzione istantanea dell’alimentazione. Rispetto ai magazzini con operatori a volte vi è un risparmio sui percorsi d’ esodo, sul sistema antincendio e sull’ illuminazione.
Dato l' elevato costo di tali impianti, l' investimento si ammortizza meglio con impiego su più turni. Anche in caso di lavoro su un turno, è comunque possibile sfruttare l’ impianto durante l’ orario di chiusura per delle routine di riposizionamento ed avvicinamento delle UDC per il turno successivo.
Il corridoio di lavoro minimo di 1,2m, aumenta in funzione della profondità del carico. Per un pallet EUR 800x1200 inforcato dal lato 800 normalmente è di 1,4m.
Le portate standard vanno da 0,5 a 1,5 Ton ma si costruiscono macchine praticamente su misura per qualsiasi portata.
L’altezza dell’ultimo livello di carico è mediamente di 15 m. Si raggiungono elevazioni anche di 40 metri. Il costo dell’ automazione è nettamente prevalente rispetto a quello della scaffalatura, pertanto più si sale con l’altezza e più si riduce il costo per posto pallet. Per costruzioni che superano i 15 metri, diventa economicamente conveniente realizzare il magazzino autoportante, vale a dire che le scaffalature sono progettate come un vero e proprio edificio considerando le azioni di sisma, vento e neve e sorreggono direttamente il tetto e le pareti laterali realizzati in pannelli sandwich monopanel. Con tale scelta non sarà possibile cambiare in seguito la destinazione d’uso dell’ edificio.
Per motivi costruttivi delle macchine, il primo livello di carico è normalmente a 800-900 mm. da terra, mentre tra la sommità dell’ ultimo pallet stoccato e la legatura superiore servono circa 500mm.
In funzione del lay-out e del numero di cicli i trasloelevatori possono essere uno per ogni corsia, oppure uno per più corsie; in questo ultimo caso il cambio corsia può avvenire mediante diverse tecniche:
La prima tecnica ad essere stata utilizzata utilizza una navetta che scorre trasversalmente nella testata del magazzino e riceve a bordo il traslo proveniente dalla corsia (sistema a ponte di trasbordo). Questo sistema necessita di una meccanica piuttosto precisa, è costoso, richiede lo scavo di una fossa da 30cm circa sulla testata. Il sistema piuttosto lento ma questo svantaggio può trasformarsi in vantaggio se sulla navetta posso eseguire delle operazioni di buffering dei pallet IN-OUT e/o operazioni di picking automatico.
Il sistema di trasloelevatori sterzanti, a mio avviso più performante, consiste in un sistema di curve e scambi di rotaie ed alimentazione in una delle testate.
- un tempo di cambio corridoio molto veloce e quindi un maggior numero di cicli realizzabili,
- la possibilità che più trasloelevatori possano cambiare corsia nello stesso momento,
- la libertà di posizionamento della postazione di manutenzione,
- il costo,
- l’ affidabilità, perché abbiamo una macchina in meno che si può fermare (la navetta di testata)
- la possibilita di inserire delle catenarie di IN/OUT in entrambe le testate;
- nella testata di cambio corsia i traslo si posizionano ortogonalmente rispetto alle corsie e quindi facilmente sfruttano le forcole o il satellite di cui sono dotati per prelevare e depositare i pallet in semplicissime posizioni dove i trasporti automatici non sono indispensabili, ciò diventa particolarmente conveniente tipicamente negli impianti a media e bassa rotazione;
- non necessitano di fossa nella testata.
Il sistema sterzante con scambi attivi però è una tecnologia di cui non tutti dispongono. Alcuni costruttori offrono quindi dei sistemi semplificati cosiddetti “a U” nei quali un traslo serve due corridoi nel qualcaso si può ottenere una riduzione del costo del magazzino ma non la possibilità di lavorare sempre con almeno una macchina in tutti i corridoi in caso di fermo tecnico.
Per un ulteriore aumento della densità di stoccaggio, e/o per aumentare la stabilità di un edificio autoportante in presenza di particolari condizioni geometriche o ambientali, le UDC possono essere gestite da forcole telescopiche speciali in doppia profondità (ogni corridoio serve quattro file di scaffali)
oppure in multiprofondità gestite da satelliti, ovvero delle unità motorizzate che scorrono su guide fissate agli scaffali.
Figurino di trasloelevatore sterzante
Video impianto con due trasloelevatori sterzanti
http://www.youtube.com/watch?v=fh-pNvAAojI&feature=youtu.be
In magazzini di altezza 6-8 metri e indici di rotazione medio bassi si può utilizzare una navetta automatica che è vincolata al pavimento e non in sommità e per questo ha liitazioni di portata, altezza e velocità.
La navetta sfrutta una combinazione di telai che abbassano le ruote longitudinali per la marcia in corsia e quelle trasversali per il cambio corsia. Ogni ordine di ruote ha un disco in acciaio di diametro maggiore che si inserisce nelle guide a U che vengono interrate nel pavimento.
Video con navetta speciale quadridirezionale:
http://www.youtube.com/watch?v=LgklUCZSfaw&feature=youtu.be
Il commissionamento negli impianti automatici
Normalmente il commissionamento, ovvero picking, ovvero il prelievo/deposito di una parte dei prodotti presenti su un pallet, avviene portando l’ unità di carico (UDC) in testata, l’ operatore esegue il commissionamento, l’ UDC viene riportata in ubicazione. Questo comporta chiaramente un doppio ciclo dei trasloelevatori. Nella maggior parte dei casi il ciclo è combinato, ovvero il traslo ad ogni ciclo porta fuori un UDC da commissionare e ricovera quella commissionata.
Vi sono casi in cui è più conveniente effettuare il commissionamento direttamente sul trasloelevatore:
¨ in modo automatico, se la morfologia delle merci da prelevare lo consente, mediante un portale dotato di ventose;
¨ in modo manuale, facendo salire a bordo uno o due operatori che non comandano il mezzo il quale esegue automaticamente il programma di lavoro già ottimizzato dal software di gestione dell’ impianto MFCS (Material Flow Control System) fermando il traslo esattamente davanti alla posizione di picking ed alla perfetta altezza ergonomica di lavoro perché conosce il numero di colli rimanenti su ogni pallet. Uno speciale sistema pick to light consente agli operatori di abbandonare la posizione di sicurezza che devono mantenere durante il movimento e prelevare la giusta quantità di colli senza possibilità di errore.
Movimentazione di merci non palletizzate
I trasloelevatori che anziché pallet movimentano colli o contenitori tramite appositi sistemi anziché le tradizionali forcole telescopiche sono chiamati sistemi MINI-LOAD.
Tipicamente questi impianti lavorano su altezze da 9 a 20 metri, con le UDC disposte in doppia profondità. Quando è richiesta una grande produttività si preferisce lavorare in singola profondità e/o adottare un secondo organo di presa in modo tale da poter movimentare più UDC ad ogni ciclo.
Anche nei mini-load vi è spesso la necessità di commissionare parti dei prodotti contenuti nei contenitori, in questo caso tipicamente i traslo estraggono i contenitori e li depositano in un buffer automatico ad anello chiuso nella testata che porta il contenitore nella postazione di picking e lo riporterà al traslo una volta eseguito il commissionamento.
Nei sistemi ad alta frequenza di prelievo si ricorre ad anelli di trasporto complessi che portano proprio davanti ad ogni operatore sia il contenitore da commissionare sia il collo di destinazione in una postazione ad alta ergonomia, attrezzata con sistema put-to-light.
Fino a quindici metri di altezza, l’imprenditore può scegliere se realizzare un edificio in calcestruzzo ed inserirvi il magazzino, anche se, normalmente, il magazzino autoportante è più economico. Per magazzini più alti, la struttura autoportante è invece la sola soluzione tecnicamente possibile.
Per magazzino autoportante si intende una scaffalatura porta pallet, portaripiani, portacassette o cantilever, progettata esattamente in funzione degli oggetti da stivare (pallet, bin, contenitori, cassette...) e della tecnologia di automazione scelta (qui parliamo di trasloelevatori ma ci sono altre tecnologie).
La scaffalatura è opportunamente dimensionata per sorreggere tetto e pareti, realizzati in pannelli sandwich in lamiera d’acciaio con isolamenti di diverso grado e spessore in schiuma poliuretanica o lana di roccia e con varie texture e colorazioni.
La progettazione, eseguita secondo le norme tecniche di costruzione, tiene conto delle forze agenti di spinta vento, carico neve, sisma, tolleranze di spostamento della struttura che sono molto stringenti (spostamento ammesso entro 1/1000 dell’altezza dell’impianto sottoposto a spinte dinamiche accidentali).
Esempi di impianti autopportanti:
Elcom (autoportante interrato con carrello trilaterale)
Posted by admin at 11/09/2022 05:25
I MAGAZZINI VERTICALI
Revisione 7 dell' 11 Settembre 2022
I VANTAGGI DEL NOLEGGIO:
- Deduce totalmente i canoni ai fini IRES senza obblighi derivanti dalla durata minima del contratto prevista dal T.U.
- Deduce totalmente i canoni ai fini IRAP, senza distinzione tra capitale ed interessi
- Vantaggio Basilea 2: grazie al noleggio, il bene utilizzato è “fuori-asset”; quindi, non necessita di corrispondente patrimonio
- Proporzionalmente al valore di riscatto garantito dal fornitore, paga canoni di importo minore rispetto ad un leasing/finanziamento
- Semplifica la gestione dei servizi accessori: manutenzione ed eventuali commodities
- Pianifica i propri budget, trasformando i costi fissi in costi variabili
- Comprende i costi di manutenzione preventiva, help desk e riparazioni full service per la durata del nolo
- Al termine della locazione si possono acquistare i beni come usato al valore di riscatto pattuito in sede di contratto oppure restituirli.
clip video disponibili ai link:
Posted by admin at 22/11/2015 23:12
PICKING DINAMICO
I sistemi dinamici per colli sono composti da file di rullini opportunamente distanziate ed inclinate per far scendere la merce verso il fronte di picking. Una volta prelevato od esaurito un collo sul fronte, immediatamente ne scende un altro dando perfetta continuità al prelievo dove, con i sistemi statici, c' è la necessità di complicati appuntamenti tra il picker e l' addetto all' abbassamento delle scorte.
Questo sistema è adatto per articoli che hanno una giacenza di almeno tre quattro colli. Notiamo infatti che dove nella scaffalatura statica in una campata troverebbero posto due pallet a terra (pari a due referenze) ed altre quattro, massimo sei referenze su due livelli a pianetti, per un totale di sei - otto articoli (semprechè ogni articolo non abbia più colli nel qualcaso il percorso si dilata drammaticamente);
nel medesimo spazio, con il sistema dinamico possiamo allocare ben 20 referenze: da 2 volte e mezza a 3 volte tanto. Grazie alle rulliere infatti ogni referenza occupa solamente il suo fronte più piccolo mentre la scorta per n ore o giorni di prelievo sta dietro.
Questo abbatte drasticamente il percorso che i commissionatori devono compiere per passare davanti a tutto il display del magazzino e comporre l' odine del cliente che stanno allestendo.
Inoltre la merce è sempre tutta disposta sul fronte degli scaffali quindi l' operatore non deve entrare con le braccia per mezzo metro a prendere i colli in seconda fila nello scaffale statico, con la necessità di usare una scala od una pedana elevabile per i livelli più alti.
Vedi il video
A volte, con decine di colli di scorta per ogni articolo, oltre alla riduzione del percorso di picking, si riesce ad ottenere anche un aumento della capienza del magazzino fino al 30%.
Ci sono diverse opzioni che permettono di applicare i telai a rullini anche a scaffalature bifronti esistenti.
Anche dove la scaffalatura esistente non fosse per nulla compatibile, possono essere inseriti dei moduli con spalle autonome
Sopra ai livelli di picking si possono disporre i pallet interi delle scorte:
- su tutte le scaffalature, a patto che le piste siano larghe come i bifronti e che tutte le corsie siano adatte alla manovra dei carrelli elevatori
- solo sulle scaffalature esterne se si utilizzano corsie differenziate, ovvero più larghe dove manovrano i carrelli e più strette dove operano i pickers, sistema che permette ai rifornitori ed ai preparatori non intralciarsi mai e quindi effettuare gli abbassamenti delle scorte contemporaneamente al picking.
Negli impianti ad alta efficienza si possono disporre i telai per ottenere un fronte di picking ergonomico che segue la naturale curva di prelievo dell' operatore; eventualmente, se la merce è particolarmente minuta, le rulliere possono essere allestite con ripiani finali che inclinano maggiormente verso l' operatore le unita di carico, migliorando l' accesso alla merce.
nelle applicazioni più spinte, ovviamente con un sensibile aumento dei costi, si completa il sistema mediante rulliere motorizzate che riforniscono di unità vuote e portano quelle riempite verso la testata di packing e/o di smistamento. Si possono anche aggiungere postazioni attrezzate per diverse operazioni che rendono lo scaffale dinamico un vero e proprio impianto semiautomatizzato.
Rivedi il video Torna all' indice
IMPILATORI DI PALLET VUOTI
In tutti i centri distribuzione il recupero dei pallet vuoti è un' operazione ripetitiva e fastidiosa per gli operatori ed è anche onerosa per l' azienda;
Questi sono alcuni modelli organizzativi :
- il preparatore che preleva l' ultimo collo dalla posizione di picking, toglie il pallet vuoto e lo deposita di coltello sulle forche o sulla pedana del suo commissionatore. Quando ha completato la sua lista porterà le UDS nella testata di precarico/spedizione e nelle vicinanze troverà le pile più o meno alte di vuoti e dovrà accatastare a mano su una di esse il proprio pallet vuoto su pile più o meno alte.
Questo modello presenta le seguenti criticità:
a) può capitare che il preparatore incappi in più posizioni in rottura di stock ma non potrà caricare sul suo commissionatore più di uno o due pallet vuoti;
b) accatastare un pallet vuoto che misura 80x120x14 cm e pesa 7-8Kg ad altezze diverse è al limite delle prestazioni fisiche di un operatore maschio ed è fuori portata per una donna;
c) le cataste possono essere alte al massimo 10 pallet - il preparatore trasmette le coordinate della posizione in rottura di stock via palmare e WMS o via telefono ed il compito di recuperare i pallet vuoti è affidato agli addetti all' "abbassamento" dei pallet pieni dalle posizioni di scorta alla poszione di picking.
Questo modello presenta le seguenti criticità:
a) ad ogni abbassamento il refiller deve raggiungere la posizione con il suo carrello retrattile o frontale a forche vuote, inforca il vuoto e lo deposita a terra nelle vicinanze, poi può raggiungere la posizione di scorta che potrebbe non essere esattamente sopra la posizione di picking ed effettua l' abbassamento per poi reinforcare il vuoto che deve portare in testata. L' operatore non compie sforzi fisici ma il tempo ciclo e le percorrenze del mezzo si dilatano drammaticamente con conseguente costo. - il preparatore trasmette le coordinate della posizione in rottura di stock via palmare e WMS o via telefono ed il compito di recuperare i pallet vuoti è affidato ad uno o più operatori dedicati dotati di carrello commissionatore che accatastano i pallet direttamente sulle forche de commissionatore per poi abbandonare nelle posizioni di recupero.
Questo modello presenta le seguenti criticità:
a) si può adottare solo in Ce.Dis. piuttosto grandi con un numero di recuperi sufficiente a garantire il lavoro a uno o più addetti;
b) accatastare un pallet vuoto che misura 80x120x14 cm e pesa 7-8Kg ad altezze diverse è al limite delle prestazioni fisiche di un operatore maschio ed è fuori portata per una donna;
c) le cataste possono essere alte al massimo 10 pallet. - Se il numero di posizioni di picking è maggiore del numero di articoli in display e si ha in dotazione un buon software WMS, è possibile utilizzare il modello 3 in differita, ovvero si deve poter lasciare in locazione il pallet vuoto per un certo tempo, i refiller devono abbassare il pallet di scorta dell’ articolo che sta andando in rottura di stock in una seconda posizione di picking PRIMA che finisca il prodotto. Si riesce così a dedicare a turno uno dei preparatori in cicli periodici di recupero pallet vuoti.
La scelta e la convenienza del passaggio da un modello all’ altro variano di continuo in relazione al volume di lavoro, alla disponibilità di mezzi e personale, al software ERP o WMS, cartaceo o in radiofrequenza, dagli accordi sindacali.
Uno dei miei Partner ha messo a punto degli impilatori automatici di pallet vuoti da installare nelle testate di precarico/spedizioni che migliorano le condizioni di lavoro e le prestazioni dei modelli organizzativi 1,3 e 4.
Ogni macchina riceve un pallet da un carrello commissionatore attraverso una speciale sezione di rulliera con gli spacchi per le forche e restituisce sulla stessa rulliera la catasta di pallet, perfettamente formattata, fino ad un massimo di 25 pallet (circa 3,7 metri in altezza).